Recognizing What is Porosity in Welding: Causes and Solutions
Recognizing What is Porosity in Welding: Causes and Solutions
Blog Article
The Scientific Research Behind Porosity: A Comprehensive Overview for Welders and Fabricators
Recognizing the detailed devices behind porosity in welding is essential for welders and fabricators making every effort for flawless craftsmanship. From the make-up of the base materials to the ins and outs of the welding procedure itself, a wide range of variables conspire to either exacerbate or relieve the presence of porosity.
Comprehending Porosity in Welding
FIRST SENTENCE:
Exam of porosity in welding discloses important understandings right into the integrity and top quality of the weld joint. Porosity, characterized by the existence of dental caries or voids within the weld metal, is a typical problem in welding processes. These spaces, if not properly addressed, can endanger the architectural stability and mechanical buildings of the weld, leading to possible failures in the ended up product.
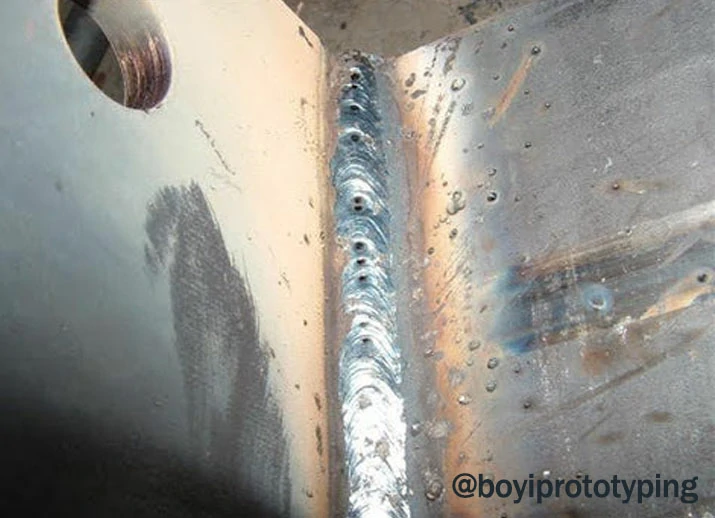
To find and quantify porosity, non-destructive screening techniques such as ultrasonic testing or X-ray inspection are often utilized. These techniques permit the recognition of interior problems without jeopardizing the integrity of the weld. By examining the dimension, form, and distribution of porosity within a weld, welders can make enlightened choices to enhance their welding procedures and attain sounder weld joints.
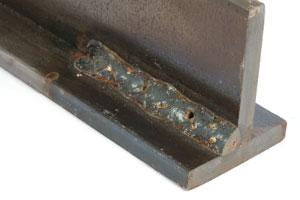
Elements Influencing Porosity Development
The incident of porosity in welding is influenced by a myriad of aspects, ranging from gas securing effectiveness to the ins and outs of welding criterion settings. One critical factor adding to porosity development is poor gas protecting. When the shielding gas, typically argon or CO2, is not efficiently covering the weld pool, climatic gases like oxygen and nitrogen can contaminate the molten metal, leading to porosity. In addition, the sanitation of the base materials plays a considerable role. Contaminants such as rust, oil, or wetness can evaporate during welding, creating gas pockets within the weld. Welding specifications, consisting of voltage, existing, take a trip speed, and electrode type, likewise impact porosity development. Making use of incorrect setups can create too much spatter or warmth input, which consequently can lead to porosity. Additionally, the welding strategy employed, such as gas steel arc welding (GMAW) see it here or shielded steel arc welding (SMAW), can influence porosity development because of variants in heat distribution and gas insurance coverage. Understanding and managing these variables are vital for decreasing porosity in welding operations.
Results of Porosity on Weld Quality
Porosity formation substantially endangers the architectural integrity and mechanical residential properties of bonded joints. When porosity exists in a weld, it produces spaces or dental caries within the product, reducing the general stamina of the joint. These spaces act as anxiety focus factors, making the weld extra at risk to fracturing and failing under lots. The visibility of porosity also weakens the weld's resistance to corrosion, as the trapped air or gases within deep spaces can react with the surrounding environment, resulting in degradation in time. Additionally, porosity can hinder the weld's ability to withstand pressure or influence, more threatening the overall quality and reliability of the bonded structure. In this post crucial applications such as aerospace, automobile, or structural buildings, where safety and security and durability are vital, the damaging effects of porosity on weld quality can have extreme effects, highlighting the significance of minimizing porosity with appropriate welding techniques and procedures.
Techniques to Decrease Porosity
In addition, making use of the appropriate welding criteria, such as the proper voltage, existing, and travel speed, is important in stopping porosity. Keeping a regular arc size and angle during welding also helps decrease the possibility of porosity.

Utilizing the appropriate welding strategy, such as back-stepping or employing a weaving activity, can likewise aid distribute heat uniformly and minimize the chances of porosity development. By executing these strategies, welders can successfully decrease porosity and create high-quality bonded joints.
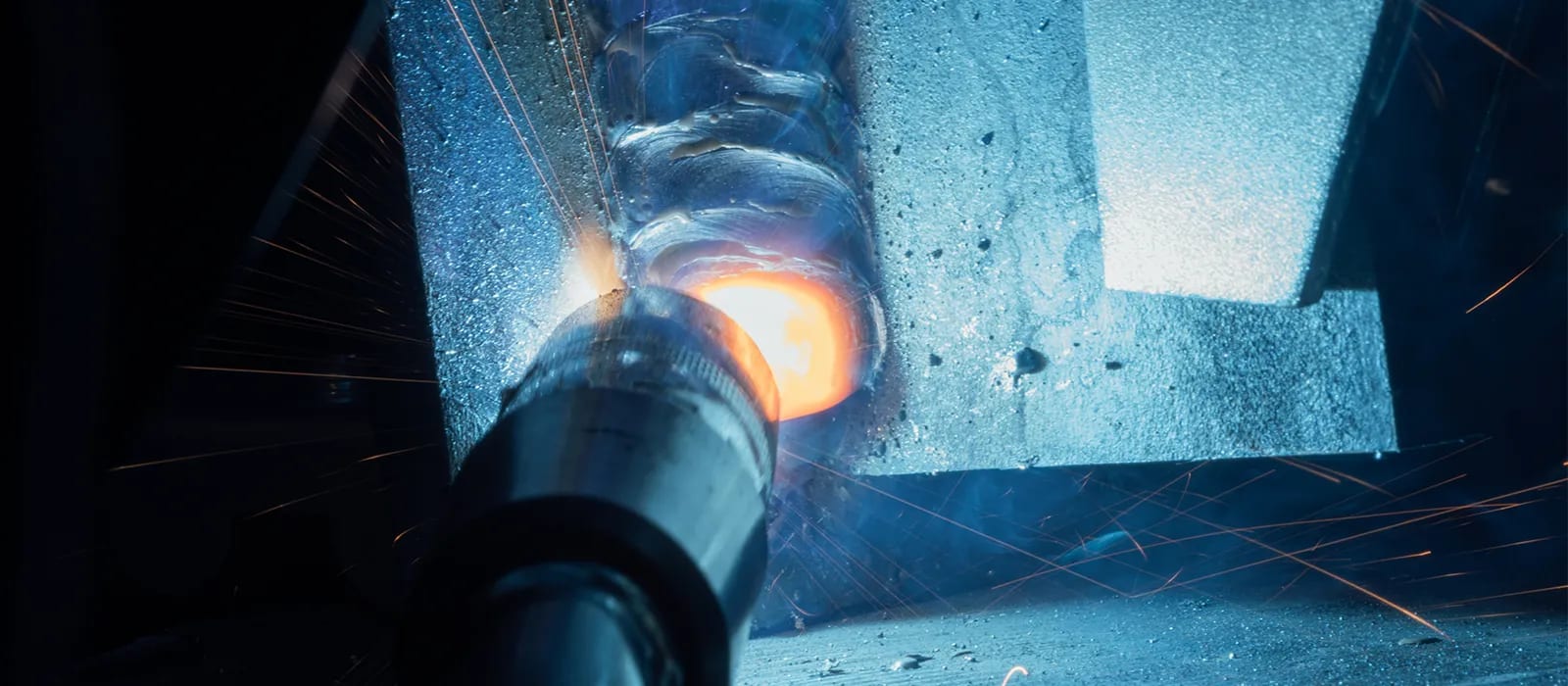
Advanced Solutions for Porosity Control
Applying advanced technologies and innovative methods plays a critical function in attaining exceptional control over porosity in welding procedures. In addition, utilizing innovative welding techniques such as pulsed MIG welding or customized ambience welding can also aid reduce porosity concerns.
Another sophisticated solution includes using sophisticated welding tools. Making use of equipment with built-in attributes like waveform control and sophisticated power sources can improve weld top quality and reduce porosity risks. Moreover, the implementation of automated welding systems with accurate control over specifications can significantly reduce porosity issues.
Moreover, integrating innovative monitoring and evaluation technologies such as real-time X-ray imaging or automated ultrasonic screening can assist in spotting porosity early in the welding process, permitting prompt rehabilitative activities. Overall, integrating these advanced services can greatly boost porosity control and improve the general high quality of bonded elements.
Conclusion
To conclude, recognizing the scientific research behind porosity in welding is vital for welders and fabricators to generate top notch welds. By determining the variables influencing porosity formation and applying methods to reduce it, welders can boost the general weld quality. Advanced remedies for porosity control can additionally improve the welding procedure and make sure a strong and reliable weld. It is essential view publisher site for welders to continually inform themselves on porosity and implement ideal methods to accomplish optimum results.
Report this page